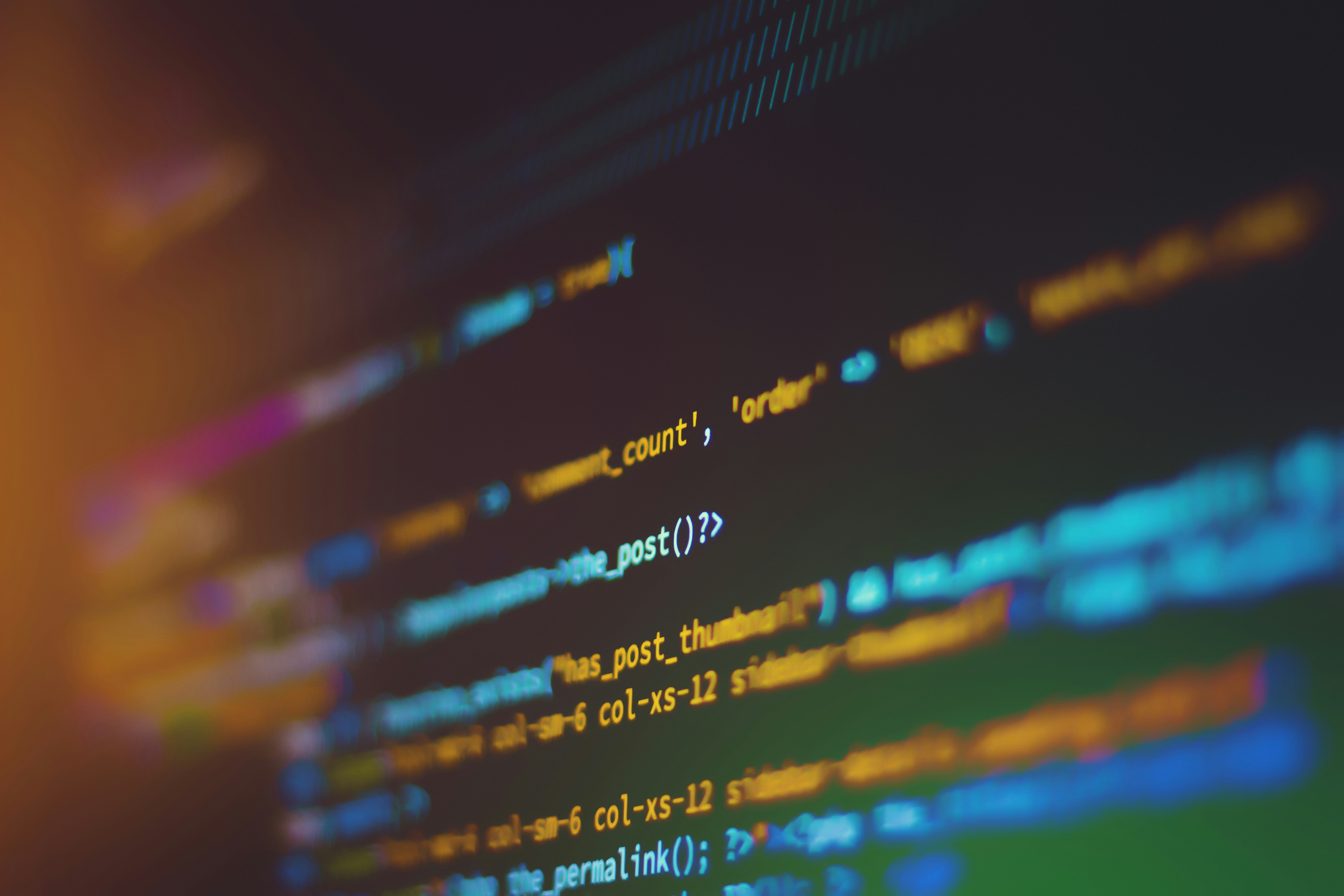
The Evolution of ERP Systems in the Manufacturing Industry: Part 1
ERP systems will undoubtedly remain at the forefront of manufacturing, empowering organizations to navigate the complexities of the modern business environment
The Evolution of ERP Systems in the Manufacturing Industry
Enterprise Resource Planning (ERP) systems have become integral to modern manufacturing, enabling organizations to streamline operations, improve efficiency, and maintain a competitive edge. The journey of ERP systems in the manufacturing sector is an interesting story of technological advancement, evolving business needs, and the relentless pursuit of operational excellence.
The Early Days: MRP and MRP II
The roots of ERP systems in manufacturing can be traced back to the 1960s and 1970s with the advent of Material Requirements Planning (MRP) systems. MRP was designed to manage manufacturing processes by ensuring that materials were available for production and products were available for delivery. It focused on three primary objectives: inventory control, production planning, and scheduling.
MRP systems, while revolutionary, had limitations. They were primarily concerned with materials and did not integrate other crucial business functions. This led to the development of Manufacturing Resource Planning (MRP II) in the 1980s. MRP II expanded the scope of MRP by incorporating additional aspects such as machine and labor scheduling, financial planning, and demand forecasting. This integration marked a significant step towards the comprehensive management of manufacturing operations.
The Emergence of ERP Systems
The 1990s witnessed the evolution of MRP II into Enterprise Resource Planning (ERP) systems. ERP systems took the integrated approach of MRP II further by encompassing a wide array of business processes, including finance, human resources, sales, procurement, and more. This integration was facilitated by advancements in computing power, database technology, and software development.
The early ERP systems were rigid, often requiring significant customization to fit the unique needs of manufacturing organizations. Companies like SAP, Oracle, and PeopleSoft emerged as pioneers in the ERP market, offering comprehensive solutions that promised to unify disparate business processes into a single, cohesive system.
The Rise of Modular ERP
As the 2000s approached, the demand for more flexible and scalable ERP solutions grew. The rise of modular ERP systems addressed this need by allowing organizations to implement specific modules based on their requirements. This approach enabled manufacturers to start with core functionalities and gradually expand their ERP systems as their needs evolved.
The modular approach also facilitated easier upgrades and reduced the complexity of system maintenance. Additionally, the emergence of internet technology paved the way for web-based ERP systems, providing remote access and improving collaboration across geographically dispersed teams.
Cloud-Based ERP: A Game Changer
The 2010s marked the beginning of a new era with the introduction of cloud-based ERP systems. Cloud technology revolutionized the way ERP systems were deployed, maintained, and accessed. Manufacturers no longer needed to invest heavily in on-premises infrastructure. Instead, they could leverage the scalability, flexibility, and cost-effectiveness of cloud-based solutions.
Cloud-based ERP systems offered real-time data access, enhanced collaboration, and improved disaster recovery capabilities. They also facilitated seamless integration with other cloud services, such as Customer Relationship Management (CRM) and Supply Chain Management (SCM) systems, further enhancing the operational efficiency of manufacturing organizations.
The Present and Future of ERP in Manufacturing
Today, ERP systems continue to evolve, driven by emerging technologies such as artificial intelligence (AI), machine learning (ML), the Internet of Things (IoT), and big data analytics. These technologies are enabling manufacturers to harness the power of predictive analytics, automate routine tasks, and gain deeper insights into their operations.
For instance, AI and ML can optimize production schedules, predict equipment failures, and improve demand forecasting accuracy. IoT devices can provide real-time data on machine performance and product quality, enabling proactive maintenance and quality control.
The future of ERP in manufacturing lies in its ability to adapt to the rapidly changing business landscape. As manufacturers increasingly embrace digital transformation, ERP systems will play a pivotal role in facilitating this transition, driving innovation, and ensuring sustainable growth.
Conclusion
The history of ERP systems in the manufacturing industry is proof of the relentless pursuit of operational excellence. From the early days of MRP and MRP II to the advent of cloud-based and AI-driven ERP solutions, the journey has been marked by continuous innovation and adaptation. As we look ahead, ERP systems will undoubtedly remain at the forefront of manufacturing, empowering organizations to navigate the complexities of the modern business environment and achieve new heights of efficiency and productivity.